Pneumatic Conveying
For more info contact us
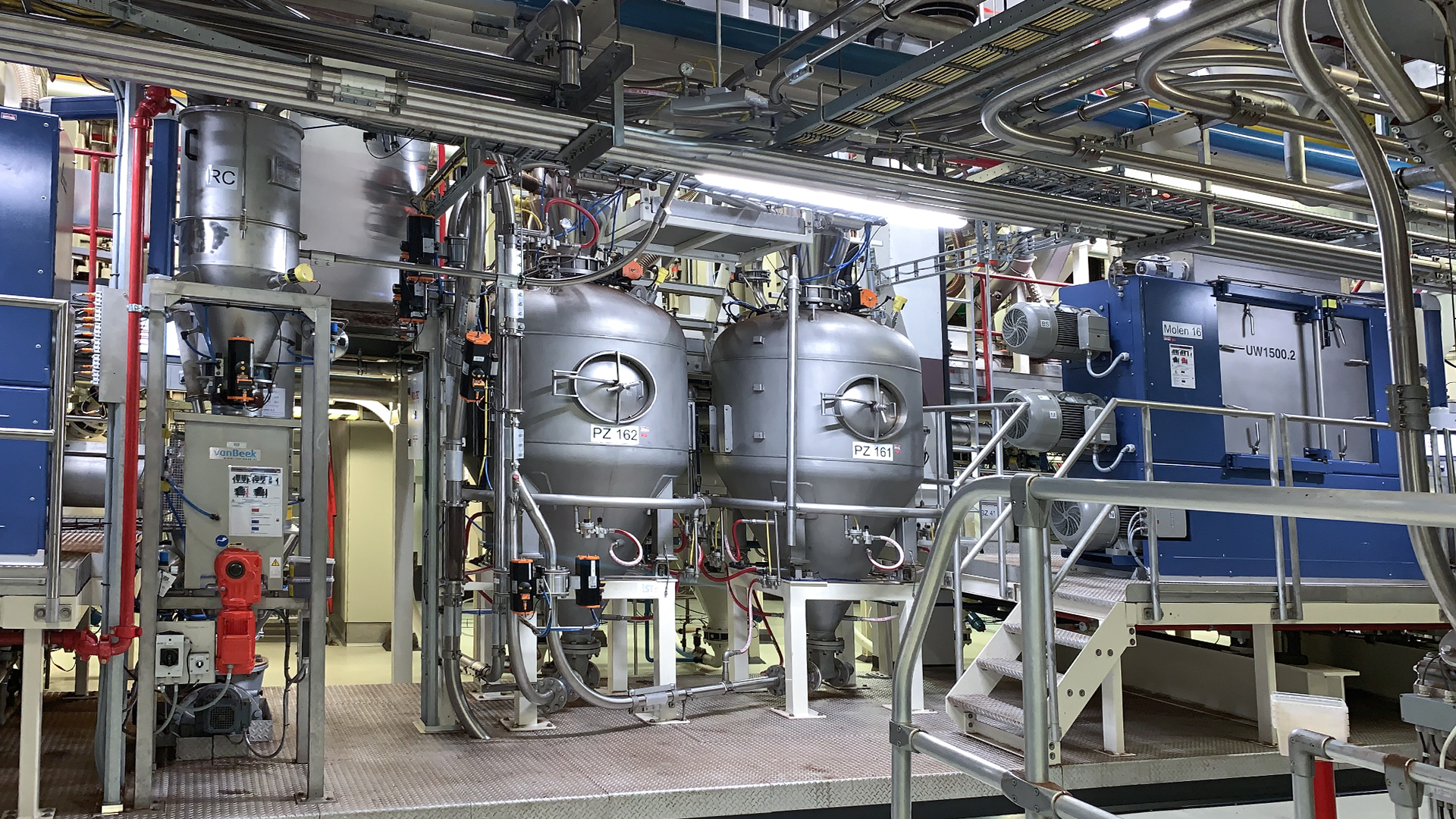
NTE Process is a global specialist in the supply of pneumatic conveying systems for powders and granules that preserve the quality of the products handled and limit the segregation phenomena of mixed product (maintaining homogenized ingredient).
DENSE PHASE PNEUMATIC CONVEYING WITH AIR ASSISTS®
NTE Process’ dense phase technology is characterized by very low conveying speeds, this results in product slugs moving compactly along the line. This method minimizes air consumption and in conjunction with the Air Assist® technology significantly reduces the use of energy. Air Assist® which is a patented system is strategically positioned along the transport pipe, it injects air at a controlled pressure and volume. It is particularly suitable for preserving fragile products, minimizing the segregation of mixed products and prolonging the operational life of lines when conveying abrasive products. The Air Assists® are suitable for both pressure and vacuum systems, they can also be retrofitted to existing systems to improve their performance, as well as to preserve the characteristics of the products sent to the bagging stations.
Benefits:
- low conveying speed
- smaller pipe diameter, reduced abrasive pipe wear
- reduced degradation of the transported product
- conveying of mixtures with reduced segregation of components
- restart of transport with tube fully charged of product (non-purging concept)
- reduced air consumption.
ECO DENSE-TRONIC®
Eco Dense-Tronic® is the patented NTE Process solution that radically changes traditional dense phase conveying through the evolution of smart technology. The use of Artificial Intelligence Air Assists® M533 enables the control of the injection flow rate of each single point and the optimal pressure profile of the gas (air, nitrogen, etc.) for the specific product conveyed. This occurs in a precise way, electronically and even remotely through the use of an advanced Artificial Intelligence.
The application of this technology is particularly suitable for conveying:
– materials whose degradation must be limited such as coffee beans, tablets, animal feed, atomized products, microencapsulated, etc.
– abrasive materials, limiting the abrasiveness of the lines as in the case of silica sand, pozzolana, limestone, ashes and products resulting from filters, slag from blast furnaces, etc.
– mixed homogenized material by limiting its segregation.
Eco Dense-Tronic® is a unique solution because it allows you to adjust the speed as wells as the air / product ratio thanks to the use of Artificial Intelligence. Benefits of this are an increase in efficiency of 40% * and a reduction in energy consumption of up to 70% *. These characteristics make the system flexible and resistant to concerns such as clogging.
For each plant equipped with Eco Dense-Tronic®, there is a CO2 savings equivalent to nearly 3,000 new trees planted in one year.
*Results achieved on specific plant configurations.
DENSE PHASE PNEUMATIC CONVEYING WITH TRANSPORTER
Over time NTE Process has optimized dense phase pressure conveying systems with transporters to handle products with high bulk density which need to be transported over long distances (such as foundry sand). The technology is proven for fragile products (such as granular sugar) as well as for mixed products (such as batches for the food industry, glass and fiberglass, ceramics, etc.).
Optimization results in dust free systems (less fines) and reduced wear of the pipes and other components (e.g., curves, receiving hoppers) thanks to the reduced conveying speed.
The NTE Process Transporters M201 can be provided in different sizes, starting from 25 liters, and they are fully certified according to various regulations in place (PED, ASME, U-Stamp etc.). The absence of internal mechanical rotating parts minimizes the risk of metal contamination and reduces maintenance costs.
“SLOW FLOW” DENSE PHASE PNEUMATIC CONVEYING
The Slow Flow NTE Process system uses a rotary valve for dense phase high pressure pneumatic conveying. It is usually applied to transfer granular products (such as rice or plastic pellets) or powders (sugar, coffee beans, etc.). This technology is typically used to continuously convey products from machines such as dryers, extruders, roasters, etc., in the presence of limited installation space.
The product is fed into the conveying line through a high-pressure rotary airlock valve, while the exclusive NTE Process “Gas Management System”, using Air Assists®, controls the volume of air used, optimizing the air / product ratio to obtain maximum efficiency and the slowest speed possible for the specific application.
DENSE PHASE VACUUM PNEUMATIC CONVEYING
The NTE Process dense phase vacuum conveying is used whenever there is little installation space under silos, hoppers, process machines or filters and it is difficult to install systems with transporters. It is also suitable to convey abrasive, mixed and / or fibrous products continuously from multiple sampling points to a single destination.
This system is designed to transfer fine powders, granules and micro components at low speed and guarantees high dust containment, as it eliminates any dispersion in the environment. The system meets ATEX regulation and can meet various regulation required for the food and pharmaceutical industries and protects products where particle size needs to be preserved.
DILUTE PHASE PNEUMATIC CONVEYING
The dilute phase is the most widely used technology in industrial plants for conveying non-abrasive and non-fragile powders and granules.
Dilute phase pneumatic conveying can be either pressure or vacuum, it moves low quantities of materials at a high velocity and low pressure. There is low concentration of product inside the conveying line as the product travels at the same speed as the air.
Dilute phase vacuum pneumatic conveying is suitable for medium-long distances, low flow rates and where product deterioration is not relevant (e.g., carbonates, flours, raw materials for the food industry, etc.).
Dilute phase pressure pneumatic conveying is suitable over medium distances for handling slightly abrasive and non-friable products as well as material with a light bulk density such as ground coffee, raw materials for loading reactors or bagging machines.
Benefits:
- simple to operate and not expensive
- requires relatively little headroom
- ideal for products that tend to compact, if non-abrasive such as resins and fibers.
NTE Process provides solutions that are easy to clean and suitable for hygienic applications.