Thanks to a team of qualified technicians, NTE Process provides a site survey service on existing systems, monitoring and scheduled or extraordinary maintenance, essential for guaranteeing correct and optimal functioning over time, as well as the quality of performance and the reliability of the systems.
For more info info contact us
Customized solutions, qualified assistance, global presence and local support.
NTE Process is a reliable partner that guarantees the efficiency of industrial plants, minimizes downtimes and takes care of installation and commissioning worldwide.
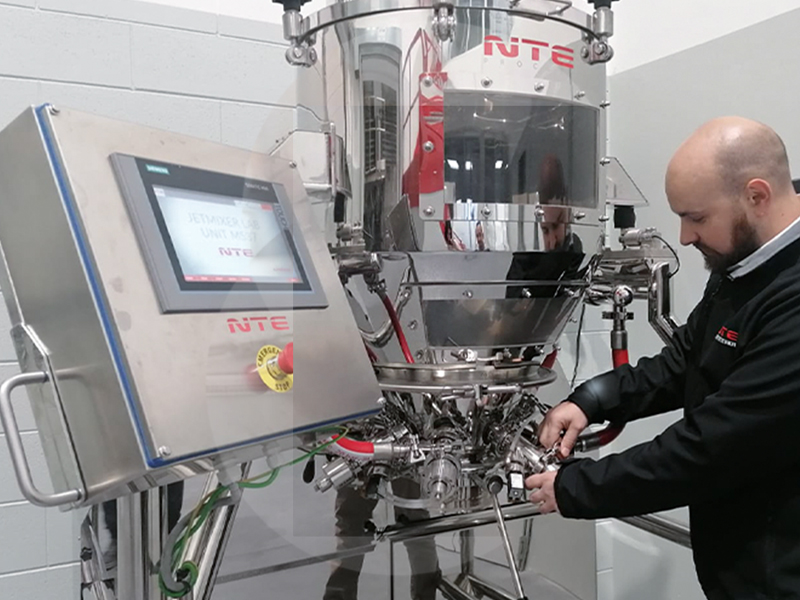
Want to know more? Download the Brochure
CUSTOMER CARE
Customized solutions and top-quality service!
The NTE Process Customer Care Department has the primary objective of monitoring customer satisfaction through continual support during all phases of the order and, subsequently, assisting them in the maintenance, management and control of the spare parts necessary for correct functioning of the plant.
Thanks to a team of qualified technicians, the company provides a site survey service for existing plants as well as scheduled or exceptional maintenance. NTE Process can monitor existing plant to ensure correct and optimal operation over time, confirming quality of performance and reliability of the systems. Furthermore, the predictive maintenance and remote assistance packages allow you to reduce downtime of the plants and improve mean time to repair through the optimization of the spare parts stock. The remote connection can allow third party monitoring by NTE Process and assistance services based on 24/7 contracts and hot lines.
The NTE Process Customer Care Team is a single point of reference that guarantees the reliability and security of a customized, time bound and proactive solution.
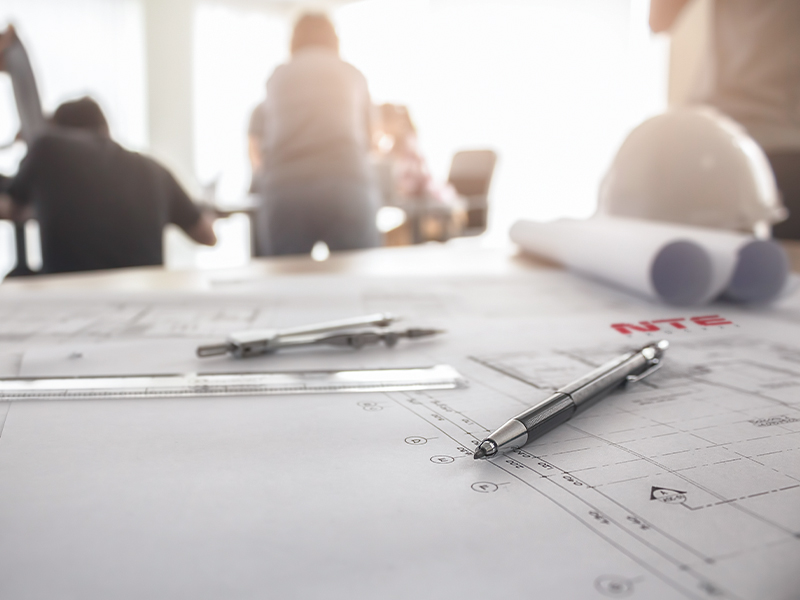
CONSULTANCY AND DESIGN
NTE Process studies the customer’s needs to create reliable and precise systems.
Thanks to the technological expertise and knowledge of the process, the company provides specific and personalized technological consultancy, to be effective for the unique characteristics of the products to handle. The approach is to provide a “turnkey” solution.
A unique Solution Provider is at your disposal from the design or check-up of existing plants, to delivery and installation all over the world, up to commissioning and start-up.
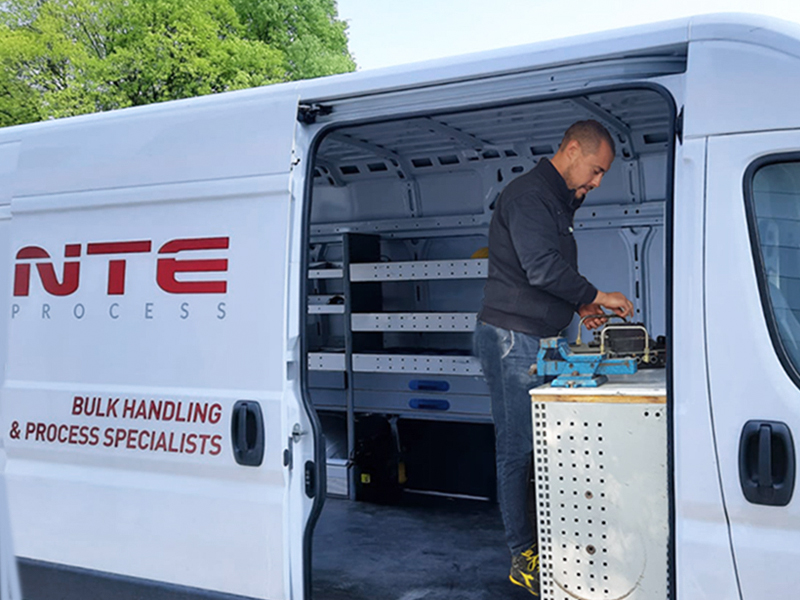
MAINTENANCE AND SPARE PARTS
To ensure the full efficiency of the system, NTE Process provides convenient assistance services, annual scheduled and preventive maintenance packages that include the visit of specialized technicians. Together with the customer, the technicians will evaluate the possible state of wear of the components and will carry out a general check to ensure proper functioning of the system. At the end of each visit, a technical report is drawn up with details of the checks performed and any improvement and / or corrective actions that must be undertaken.
Preventing any breakdowns also means significantly reducing maintenance costs, ensuring the full efficiency of the systems and avoiding unscheduled plant shutdowns and loss of production.
The remote assistance service can be included in the quotation of a new system or installed at a later date. It is possible to remotely monitor the plant directly from the NTE Process headquarters and to assess equipment performance levels allowing intervention to prevent or resolve critical issues promptly.
The NTE Process Components and Spare Parts Department ensures the supply of original materials and the customer is provided with complete lists of spare parts, ensuring limited procurement and shipping times.
Specific software installed on the system warns the customer about the need to replace a component in order to prevent accidental shutdowns of the systems, and to act promptly in the event of an emergency.
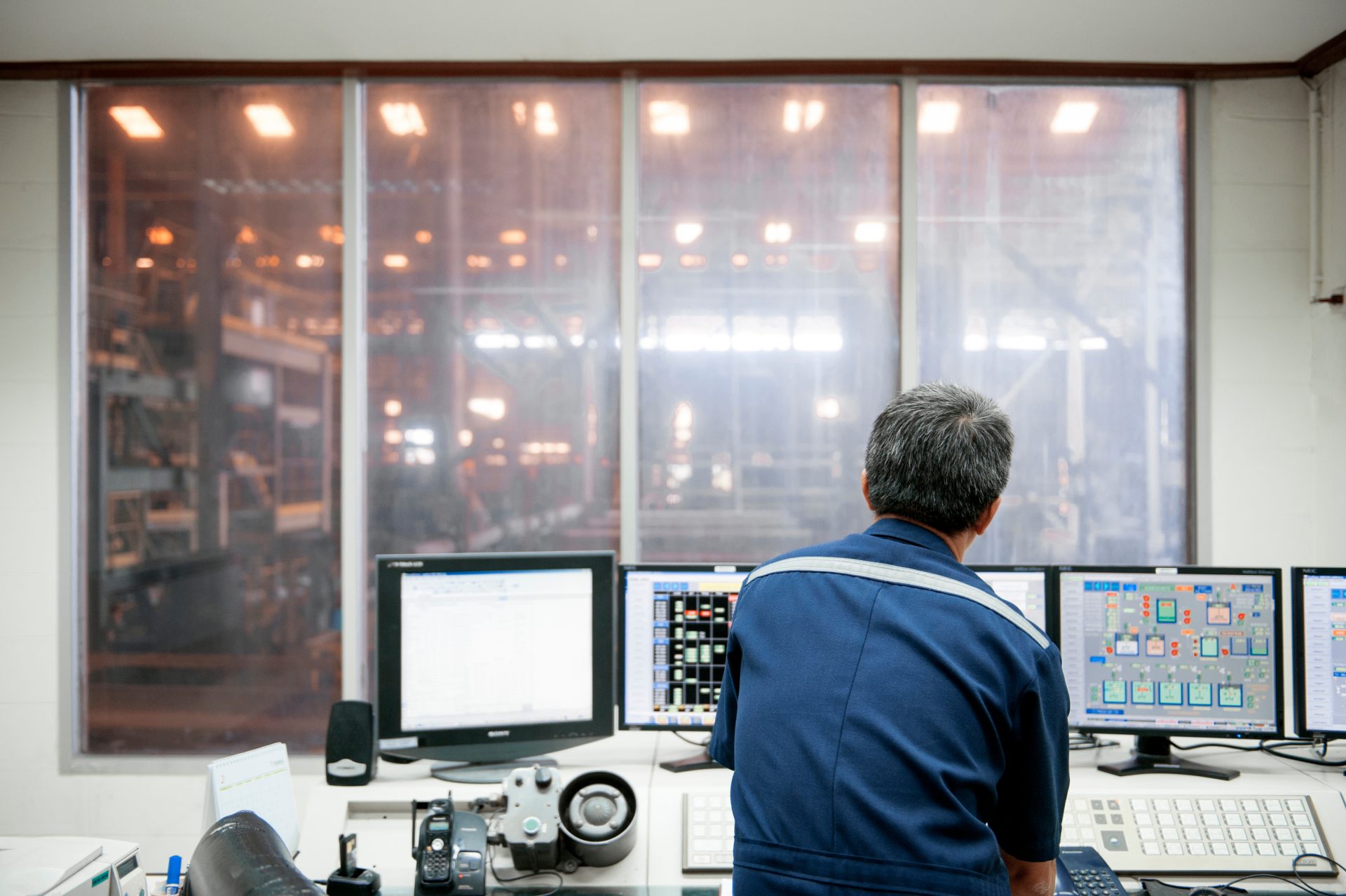
AUTOMATION
The NTE Process Automation Department provides customers with a wide range of solutions for managing any type of production process:
- Full automation engineering, which includes electrical and control panel design;
- Software and functioning specifications;
- HMI, process flow charts and predictive maintenance systems;
- Manuals for operators;
- Training and assistance for the customers production team.
NTE Process creates intuitive and functional video guides. Clear operation standards allow the customers associates to manage the system with limited training time. Thanks to the experience in pneumatic conveying and bulk handling, NTE Process manages complex recipes, as well as monitoring and traceability of components. The customer has access to primary and secondary data, through an SQL database and the use of other softwares. Barcodes and other types of material coding are used in order to avoid incorrect inputs by the operator. Traceability of ingredients and finished product can be controlled and flagged by the system with visual, audio or hard stop indicators for operator.
The solutions are open and programming is simple, immediate, and tailored to the specific applications required by the customer. The code is documented and described in order to give maintenance personnel a system that is easy to manage and monitor.
NTE Process cooperates with the most important software and hardware suppliers for each subsystem of the plant:
- Motion Controls
- PLC
- I/O List
- HMI interfaces
- PC Based Controls
- SCADA.
Particular attention is paid to the choice of bus systems, from Profibus and Profinet to DeviceNet and Ethernet, based on the specific needs of the systems.
After-sales assistance is provided all over the world thanks to a wide range of remote tools, using the web, GSM, UMTS, and the traditional telephone network supported with a 24/7 assistance service.